摘要
初始殘餘應力是造成工件加工變形的主要原因,被認為是影響加工質量的重要方麵之一。對坯料內部初始殘餘應力分布的推斷對加工變形控製具有重要意義。由於現有的殘餘應力檢測方法存在原理誤差,在實際應用中仍存在挑戰。針對初始殘餘應力場的檢測問題,提出了一種結合監測數據和機理模型的初始殘餘應力場推斷方法。采用加工過程監測數據表征不平衡殘餘應力的宏觀表征,采用有限元數值模型作為機構模型,解決了解析機構模型難以建立的問題;針對學習模型和機製模型相結合的梯度下降問題,引入了策略梯度法。最後,根據監測數據與機理模型融合的方法,通過迭代計算得到初始殘餘應力場。驗證結果表明,所提出的初始殘餘應力場推斷方法能夠準確、有效地反映實際加工過程中的加工變形。
簡介
在毛坯製造過程中,由於熱梯度、力載荷和相變等原因,工件內部不可避免會產生初始殘餘應力,初始殘餘應力的存在會嚴重影響工件的加工質量,在航空製造領域尤為關鍵。以飛機結構件用的高強度鋁合金預拉伸板為例,坯料一般要經過鑄造、淬火、熱軋、鍛造、預拉伸、時效等工序。在製造過程中,毛坯會經曆不均勻的溫度場,產生不均勻的彈塑性變形。因此,在毛坯內部會產生殘餘應力。在加工過程中,由於材料的去除,具有初始殘餘應力的毛坯的初始殘餘應力將被打破。工件會發生變形,從而達到新的平衡狀態。在飛機結構件領域,加工變形問題尤為嚴重。飛機結構件的特點是尺寸大,材料去除率高(高達95% [1,2])和薄壁,會導致零件加工變形較大,變形嚴重將直接導致零件報廢[3.,4].相關研究表明,毛坯內部的初始殘餘應力是造成結構件加工變形的重要原因之一[5- - - - - -8].因此,獲得初始殘餘應力場分布對加工變形控製具有重要意義。
由於初始殘餘應力場的分布具有空間分布複雜、形式多樣、受坯料尺寸影響分布規模大的特點,因此殘餘應力場的推斷具有很大的挑戰性。目前獲取殘餘應力的方法主要分為破壞性檢測和非破壞性檢測兩種,這兩種方法的主要原理是檢測殘餘應力的一些間接物理量,並通過反解題過程獲得殘餘應力。然而,現有的檢測方法在實際應用中仍存在一些問題。如粘貼應變片進行破壞性檢測技術,這種方法存在檢測精度低、檢測結果可靠性差、隻能檢測局部殘餘應力等問題。在無損檢測技術中也存在一些問題。超聲波檢測技術容易受到材料內部缺陷的幹擾,檢測結果的可靠性不高。由於x射線穿透深度有限,隻能檢測工件表麵的殘餘應力。中子衍射技術具有較強的穿透能力,但這種方法的探測原理直接導致了探測成本高的問題。由此可見,現有檢測方法在實際應用中仍然存在很多問題。
為了獲得坯料內部的初始殘餘應力,本文提出了一種結合監測數據和機理模型的初始殘餘應力推斷方法。對加工過程中的變形力進行監測,采用策略梯度算法將監測數據與有限元機構模型結合,推斷出初始殘餘應力場。本文提出的初始殘餘應力場推斷方法的總體思路如圖所示1.采用神經網絡作為發生器產生初始殘餘應力場;利用有限元機構模型計算產生的初始殘餘應力場對應的變形力;將得到的變形力與真實的變形力數據進行比較,得到偏差,然後根據偏差調整發生器,重新生成更接近真實數據的初始殘餘應力。這樣迭代,直到收斂,即偏差滿足一個閾值,最後得到一個精度要求的初始殘餘應力場。
相關工作
工件內部的初始殘餘應力是造成加工變形的主要原因,它嚴重影響工件的加工質量。因此,對工件進行檢測,了解工件內部的初始殘餘應力,對控製加工變形,提高加工質量具有重要意義。目前在殘餘應力檢測方麵應用比較廣泛的技術主要分為兩類:破壞性檢測技術和無損檢測技術[9].
無損檢測(NDT)可以在不損傷被測對象的情況下實現。目前主流的無損檢測方法主要有x射線衍射法[10,超聲波法[11- - - - - -13,中子衍射[14)等。與破壞性檢測技術相比,該無損檢測技術具有對被測對象不造成損傷的優點。但是,受限於無損檢測的檢測原理和特點,這些檢測技術還存在一些不足。x射線衍射測量的深度較淺,檢測區域局限於材料的表麵和亞表麵,且對材料表麵的處理比較敏感,表麵粗糙度和表麵曲率都會影響測量精度。此外,由於測量空間的限製,大型結構件無法測量[15].與x射線衍射法相比,中子衍射法具有穿透深度更大的優點,可以檢測大尺寸材料的內部殘餘應力;但設備的建設和運行成本較高,嚴重影響了中子衍射法的適用性,在工業領域無法實現大型零件的原位測量[16].超聲法測量殘餘應力主要是基於聲彈性理論。當超聲波通過含有殘餘應力的材料時,由於殘餘應力的存在,聲速會發生變化,通過分析計算聲速的變化可以得到材料內部的殘餘應力。因此,超聲波法的測量效果取決於材料微觀組織的均勻性,材料內部的缺陷會嚴重影響測量精度[17].
破壞性試驗為了獲得殘餘應力,會對被試物造成損傷。該方法需要去除被測物體局部的材料,釋放殘餘應力,得到局部應變,根據應變數據得到相應的殘餘應力。破壞性檢測技術主要有以下幾種方法:盲眼鑽井[18,19是目前應用比較廣泛的一種簡單快速的方法,該方法是在被測物體的測量區域內鑽孔產生變形,用應變片測量小孔周圍的變形,根據測量數據計算出該區域內的殘餘應力。層去除方法[20.]比盲孔鑽更具破壞性,在盲孔鑽中,整個工件通過一層一層地銑削被測對象而變形。用應變片測量工件的變形數據,最後根據應變片的數據計算工件的殘餘應力。縮進法[21]是根據材料表麵硬度與殘餘應力的反比關係來求解殘餘應力。該方法與盲孔鑽削除層法相比,對工件的損傷小。分切法[22],類似於盲孔鑽孔,是通過加工被測物體上的狹縫來釋放殘餘應力,然後通過測量指定位置的應變來計算殘餘應力。上述破壞檢測技術都需要對工件進行破壞,根據Saint-Venant原理隻能得到局部殘餘應力。雖然壓痕法對工件的損傷較小,不需要使用應變片進行檢測,但由於硬度測量精度低,且被測物體表麵存在塑性區,通過硬度反向推斷殘餘應力的精度也不高。
為了彌補傳統無損檢測和無損檢測技術的不足,提出了相關的檢測方法,提高了傳統檢測技術的適用性。23]提出了一種結合檢測表麵殘餘應力和殘餘應力平衡方程的殘餘應力推斷方法。Wang等[24]提出了一種通過x射線技術測量表麵某些點的有限殘餘應力來求解完整表麵殘餘應力場的模型。Hatamleh等人[25]通過引入聯合概率密度函數,量化x射線探測結果的不確定度,提高數據的可靠性。Chukkan等[26]提出了一種在模擬環境下利用中子衍射法有限探測數據進行迭代求解的方法,從而獲得滿足精度要求的殘餘應力。Farrahi等人[27]提出了一種基於艾裏應力函數的殘餘應力場反求方法,並通過對焊接板中存在的殘餘應力的有限測量重建了殘餘應力場。這些研究雖然提高了傳統檢測技術的適用性,但並沒有在原理層麵上對傳統檢測技術進行改進,因此仍然存在檢測精度低、成本高的問題。
上述解大多是根據殘餘應力與實測量之間的機理關係建立機理模型,再根據建立的機理模型求解殘餘應力。由於機構模型是對實際情況的簡化,當實際情況比較複雜時,機構模型的性能往往不能令人滿意。因此,基於機構模型的求解方法對於複雜的殘餘應力場誤差較大。隨著人工智能技術的不斷發展,逐漸在不同學科產生了變革性的成果[28- - - - - -30.].然而,人工智能技術的出色表現往往離不開大量的數據。在很多實際的情況下,收集數據的成本往往很高,我們難免會麵臨缺乏數據的困境。在數據不足的情況下,大多數人工智能技術都會存在魯棒性不足的問題。
為了解決人工智能在複雜情況下、海量數據需求下的機構模型精度問題,將機構模型與機器學習融合的新思路已經成為一種有效的解決方案。由於機製模型反映了數據的自然規律,通過機製模型與機器學習的融合,可以利用機製模型中的先驗知識來指導機器學習模型的訓練,放大訓練數據的信息量,降低對機器學習模型數據量的需求。關於機製模型與機器學習模型的融合,已有一些研究。納塔尼爾等[31]利用神經網絡求解仿真模型的最優參數,提高了仿真模型的計算精度。Raissi等[32]提出了一種物理信息神經網絡,可以解決物理公式中的偏微分方程問題,實現了機器學習與機構模型的結合,提高了機構模型的適用性。Michael等[33]將拉格朗日力學機製模型與神經網絡相結合,建立了深度拉格朗日網絡,可以在保證物理合理性的同時,高效地學習具有深度網絡的力學係統的運動方程。Greydanus等[34]根據哈密頓力學理論,通過無監督學習訓練了遵循能量守恒的機器學習模型,與傳統方法相比,可以直接從數據中學習哈密頓力學公式。
對於推斷問題,工件初始殘餘應力場、工件內部初始殘餘應力與變形數據之間的物理關係複雜,難以建立機理關係的解析機理模型;現有的數據驅動和機構模型融合方法大多在機構模型已知的情況下使用。因此,現有的數據驅動和機構模型融合方法仍不足以解決初始殘餘應力問題。
針對現有方法的不足,本文將通過有限元法建立初始殘餘應力與變形力之間的數值模型。由於有限元數值模型從殘餘應力到變形力的計算過程不可微,數據驅動模型很難通過梯度下降法進行更新,這給數據驅動模型與機構模型的結合帶來了一定的困難。為了解決這一問題,我們將研究策略梯度算法,實現數據驅動模型與機製模型的融合。
變形力與殘餘應力的關係
在實際加工過程中,工件是用夾具夾緊的。由於加工過程中工件的材料被去除,工件內部原有平衡的初始殘餘應力被打破,工件-夾具係統會被夾具平衡,所以反作用力會被夾具反映出來,這裏反作用力定義為變形力[35],可視為工件變形的阻力。為了測量變形力,設計了專用夾具和夾具布局,如圖所示2(a).通過三個固定夾緊點形成固定夾緊區,對工件的六個自由度進行約束。根據工件的裝夾方式,我們將工件的一半作為簡支梁進行受力分析,如圖所示2(b)和(d)。
工件的變形力是由工件內部初始殘餘應力不平衡引起的,變形力可以看作是工件內部初始殘餘應力的宏觀表征量。工件內部的不平衡殘餘應力疊加,以彎矩的形式作用在工件上(z \ ({} _ {} \),\ ({M} _ {x} \)),造成工件變形。工件受夾緊點約束,變形趨勢作用於夾緊點產生變形力(\ ({F} _ {1} \),\ ({F} _ {2} \)).
為了便於描述變形力與初始殘餘應力之間的關係,我們將工件的受力狀態簡化為兩個維度,如圖所示2(c).工件的材料去除後,內部不平衡殘餘應力形成彎矩,造成工件變形。沿厚度方向對各截麵上的初始殘餘應力進行積分,積分公式如1):
在哪裏σ為工件的內應力;一個而且b分別為工件上表麵和下表麵到中性表麵的距離。
從情商。1)時,可以看出,不平衡初始殘餘應力相對於中性區形成了彎矩。如圖所示2(c)、如果工件不受約束,工件會變形。當工件被夾緊約束時,彎矩引起的變形趨勢以變形力作用在夾緊點上。平衡方程由圖可知2(c):
同時,不平衡初始殘餘應力與工件夾緊力之間的關係可由Eq. (1)和Eq. (2),如Eq. (3.):
機理模型與監測數據的結合
在上一節中,我們通過Eq. (3.).由於初始殘餘應力是以場的形式存在的,因此不容易將Eq. (3.),用於整個工件。為了解決這一問題,本文利用有限元方法建立了殘餘應力對變形力的作用機理模型。主要方法是建立有限元模擬環境下初始殘餘應力與變形力之間的機理模型。在仿真環境中向工件添加初始殘餘應力,可以在仿真過程中獲得初始殘餘應力對應的變形力。本文建立了數值機理模型來代替解析機理模型,實現了初始殘餘應力與變形力的建模關係。
該方法以工件加工過程中的變形力數據為基礎,結合有限元數值機構模型,采用數據驅動方法對工件內部初始殘餘應力場進行迭代求解。本文提出的初始殘餘應力求解方法流程圖如圖所示3..首先,由神經網絡和高斯多峰擬合函數組成的殘餘應力發生器初步產生隨機的工件初始殘餘應力;將產生的初始殘餘應力作為有限元數值模型的輸入,分析計算相應的變形力。然後將數值模型計算出的變形力與實際變形力進行比較,得到偏差。最後,利用誤差反向傳播更新神經網絡的權值,調整殘餘應力發生器輸出的初始殘餘應力,使其更接近期望值。不斷重複,直到偏差在預設誤差範圍內最小化為止。
該方法首先利用神經網絡生成初始殘餘應力函數的係數,由函數係數確定初始殘餘應力。對輸入固定的工件采用神經網絡,根據誤差的大小更新權值來調整神經網絡的輸出。實際情況下,厚度方向的殘餘應力遠小於寬度方向和長度方向的殘餘應力,工件的加工變形主要受長度方向和寬度方向的殘餘應力影響,因此厚度方向的殘餘應力可以忽略不計。如圖所示4,為典型的工件內部初始殘餘應力分布曲線[36].從圖中可以看出,工件內部的初始殘餘應力沿厚度方向呈多峰連續變化。根據殘餘應力沿厚度方向變化曲線的特點,采用高斯多峰擬合函數進行擬合。使用高斯多峰擬合函數有很多優點,即可以用較少的參數表示更多離散的殘餘應力值,這對神經網絡非常重要,並且可以很容易地考慮物理先驗,從而得到更好的解。本文使用的高斯多峰擬合函數如Eq. (4):
鋁合金預拉伸板的長度和寬度遠大於厚度,製造過程中的淬火時效處理效果與預拉伸板的中性平麵對稱。因此,預拉伸板的初始殘餘應力可視為沿中性麵對稱分布,滿足應力平衡條件[20.].為了減小求解空間的大小,提高算法的效率,根據初始殘餘應力的分布特征,將初始殘餘應力高斯多峰擬合函數設為偶數函數。並根據應力平衡條件對發電機進行約束。如前文所述,我們利用先驗數據和知識,提前定義初始殘餘應力場擬合函數,縮小初始殘餘應力場求解值與目標值之間的差距,可以有效提高求解效率和精度。
由上可知,發生器首先生成多峰高斯擬合函數的擬合係數。得到擬合係數後,即可確定初始殘餘應力分布曲線。然後將初始殘餘應力函數輸入到有限元數值模型中,計算相應的變形力。將數值機構模型得到的變形力與實際加工環境中的數據進行比較,計算出誤差。采用均方根誤差(RMSE)來測量實際數據與求解數據之間的差值,並在發生器網絡中反向傳播。然後通過連續迭代調整網絡的權值,使偏差最小化(\ (L \))輸出結果與實際數據之間((\ D {} _ {val} \)).這是一個典型的優化問題,優化目標如下所示5):
在哪裏\ ({\ varvec {c}} \)初始殘餘應力函數的係數是否由神經網絡生成器生成,其值是否由神經網絡權值決定\ ({\ varvec{\ω}}\),c h \ ({} _ {} \)是初始殘餘應力函數的係數之間的映射嗎\ ({\ varvec {c}} \)和變形力。
本文提出的求解方法涉及有限元數值機製模型,從初始殘餘應力到變形力的過程不可微,梯度下降難以計算。為了解決這個問題,在強化學習的啟發下,策略梯度算法[37,從而解決了該問題,實現了監測數據與機構模型的融合。主要思想是輸出值(即係數\ ({\ varvec {c}} \))的神經網絡變換為高斯分布,且係數\ ({\ varvec {c}} \)可以從高斯分布中采樣,產生殘餘應力,並計算變形力偏差。然後定義獎勵函數,得到獎勵的統計期望。最後,根據最大獎勵的優化目標更新權重。政策梯度的具體方法將如下所述。
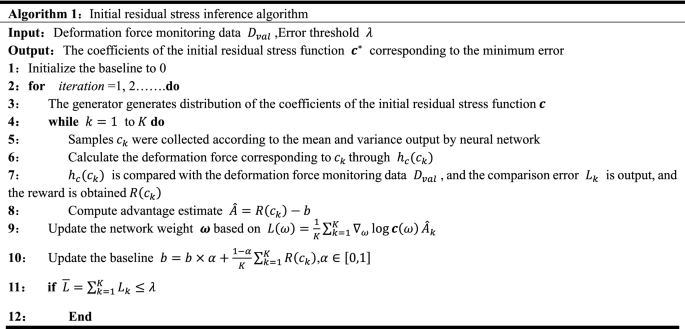
根據策略梯度的思想設置了初始殘餘應力場的推斷過程。如圖所示3.,則神經網絡的輸出為均值μ擬合函數的係數和對應的方差σ,服從高斯分布。獲得輸出後,\ (K \)根據輸出的均值和方差進行采樣次數,得到擬合係數的樣本。相應的\ (K \)擬合係數樣本可獲得初始殘餘應力樣本。計算初始殘餘應力樣本對應的獎勵(即負誤差),得到獎勵的期望。可以發現,上述問題是一個優化問題,優化目標為最大報酬期望。優化目標如下式(6),其中獎賞(\ (R \))計算為負誤差(l),也就是說,\ (R = 1 / L \).根據REINFORCE rule [37]時,我們可以得到更新後的權值梯度如Eq. (7).因此,當我們獲得獎勵期望時,我們可以通過計算得到梯度來更新神經網絡的權值,調整輸出。
梯度的無偏經驗估計如Eq. (8):
在哪裏\ (\ widehat{一}= R \離開({c} _ {k} \右)- b \)是優勢估計,b是基準,它的值是之前獎勵的指數移動平均值。該基線可以加快收斂速度,提高收斂精度。\ (K \)是每次迭代中根據均值和方差抽樣的樣本個數。\ (R \離開({c} _ {k} \) \)每個樣品的獎勵在嗎\ (K \)樣本。
該算法的偽代碼如算法1所示。變形力數據集((\ D {} _ {val} \))和誤差閾值(\λ(\ \))輸入到算法中,算法將自動進行迭代求解,直到誤差(\(\眉題{L} \))小於閾值(\λ(\ \)).初始殘餘應力函數的係數(\ ({{\ varvec {c}}} ^ {*} \))對應於變形力數據((\ D {} _ {val} \)).
案例研究與驗證
本文提出的方法在仿真環境和實際加工中都得到了驗證。在仿真環境中,設定基準初始殘餘應力場為地麵真值,通過有限元計算得到基準初始殘餘應力場的變形力。根據設定的初始殘餘應力下產生的變形力推斷出初始殘餘應力,並將得到的初始殘餘應力與地麵真實殘餘應力進行比較,驗證計算結果的準確性。在實際加工環境下,根據實際加工過程中的變形力監測數據求解工件內部的初始殘餘應力場,並基於該方法推斷工件內部的初始殘餘應力場。由於初始殘餘應力不符合實際情況,我們將實際加工過程中采集到的變形數據與根據推斷的初始殘餘應力場計算出的相應變形數據進行對比,驗證了解的正確性。
仿真環境下的理論驗證
為了便於比較、驗證和說明,本文將三維實體簡化為二維薄板作為加工對象,在仿真環境下進行理論驗證。
通過ABAQUS二次開發,在仿真環境中構建10 mm × 100 mm的二維平麵,工件單元為四邊形單元。在滿足有限元計算精度的前提下,設定單元離散尺寸為1 mm × 1 mm,材料性能以航空領域常用的飛機結構件7050-T7451鋁合金為基礎設定。具體參數如表所示1.
有限元模擬分析的主要原理是將連續的求解域離散化為單元的組合。因此,在仿真環境下工件內部的初始殘餘應力場是離散的。工件內部的初始殘餘應力沿厚度方向連續變化。為了在仿真環境中實現工件初始殘餘應力的合理疊加,將工件沿厚度方向分層,並將沿厚度方向線性變化的初始殘餘應力場按分層數離散化。然後,將離散化的應力值應用到各層的單元網格上,實現仿真環境中具有初始殘餘應力的工件的建模。為了使理論驗證時的初始殘餘應力場接近實際情況,相關研究實驗中檢測到7050-T7451鋁合金坯料的初始殘餘應力[36,並在仿真環境中進行設置,如圖所示5一個。
在加工過程中,工件變形力的監測主要是通過在工件夾具上安裝力傳感器來實現的。在仿真環境中,通過在工件監測點增加一個地彈簧來模擬力傳感器,並提取彈簧的應變數據來獲得工件的變形力。為了保證彈簧對工件的約束作用,將監測點的彈簧速率設為較大的值,即彈簧速率為50000 N/mm。在仿真環境中參照實際加工情況下工件的裝夾方式設置邊界條件。如圖所示5A,在中間位置的單元節點工件上設置固定約束,約束工件的6個自由度,固定工件的空間位姿。在工件兩端的角落處設有地彈簧,用於固定工件,測量工件的變形力。
在加工過程中,隨著加工的進行,被去除材料所含的殘餘應力從工件內部原本平衡的殘餘應力場中剝離出來,導致殘餘應力場不平衡。為了在仿真環境中模擬工件的材料去除過程,基於ABAUQS仿真平台,采用生死元法對加工過程中的材料去除進行模擬。
實際加工是一個連續的動態過程。隨著加工的進行,工件的材料沿著厚度方向一層一層地去除。在材料去除過程中,變形力會不斷變化,因此需要模擬工件的連續加工過程,記錄變形力的變化過程。通過在仿真環境中建立連續的分析步驟,對工件的時間序列動態加工過程進行仿真。ABAQUS的分析步驟是通過二次開發設定的,每個分析步驟對應於工件每一層的單個槽的加工,根據加工槽的數量設定多個連續的分析步驟,以模擬工件順序的動態加工過程。由於工件的齧合尺寸為1mm,因此加工層數為7層。每層銑削5個槽,每個分析步驟隻銑削1個槽,總共是35個分析步驟。仿真分析結束後,ABAQUS仿真軟件會生成一個.odb文件,其中包含仿真環境建模數據和有限元分析結果。我們通過Python腳本訪問。odb文件,提取模擬過程中產生的變形力數據,並保存為。csv文件格式。具體流程如圖所示6
根據變形力數據,推導出變形力對應的初始殘餘應力場。如圖所示7,經過連續迭代求解,求解結果最終收斂。以迭代誤差最小的求解結果作為輸出。
所提出的推斷方法的輸出是初始殘餘應力場的分布(即均值和方差)。為了更合理地評價輸出結果的有效性,將均值對應的變形力與基準初始殘餘應力對應的變形力進行了比較。如圖所示8,真實值為基準初始殘餘應力場對應的變形力(圖5(a))。解為推斷出的初始殘餘應力對應的變形力。Error表示真值與解之間的差值。從圖中可以找到8彈簧1和彈簧2提取的變形力基本相同,這主要是因為工件的結構基本對稱(如圖2所示)5(b)),工件內部初始殘餘應力場呈對稱分布(如圖5(a))。本實驗采用二維截麵,變形力較小。對比結果表明,最大誤差不超過0.30 N,最小誤差接近0.0003 N,平均誤差為0.105 N,表明了求解結果的有效性。
在加工過程中,工件內部不平衡的殘餘應力會引起變形力。當加工後工件的夾緊約束被釋放時,工件就會變形。因此,工件的最終加工變形相當於工件的變形力,可以反映工件內部的初始殘餘應力水平。我們將求解結果對應的變形與基準初始殘餘應力場對應的變形(如圖5(a)驗證求解結果的有效性。我們根據圖中所示的位置提取變形5(b).工件初始殘餘應力引起的變形主要是翹曲,因此我們提取了在Y方向為工件的變形量。
相對變形數據如表所示2,其中求解時的變形為解出的初始殘餘應力場對應的變形。地麵真值是基準初始殘餘應力場對應的變形。根據表中數據2,工件的變形兩頭大,中間小。測點1、2、3的變形與測點6、5、4相似。這主要是因為工件幾何結構對稱,工件內部的初始殘餘應力分布也是對稱的。此外,解的變形與地麵真實值之間的差異很小。地麵真實值與求解變形值之間的最大誤差僅為0.02462 mm,最小誤差為0.00134 mm,平均誤差為0.01132 mm。
目前的初始殘餘應力場解是基於銑削深度為7 mm時的變形力。為了進一步驗證求解結果的有效性,將推斷方法得到的初始殘餘應力場應用到仿真環境中,計算銑削深度為8mm時的變形力和變形量,並將該值與基準初始殘餘應力場對應的數據進行對比(如圖5(a)),這意味著我們使用推斷的初始殘餘應力來預測未來的加工趨勢。
數字9展示了銑削深度為8mm時的變形力對比圖。經對比,最大誤差為0.096 N,最小誤差為0.008 N,變形數據見表3..最大誤差為0.0354 mm,最小誤差為0.0037 mm,平均誤差為0.0186 mm。
為了進一步驗證求解結果的有效性,對不同基準初始殘餘應力場進行了求解和分析。如圖所示10,可以發現對於不同的初始殘餘應力場都有很好的求解結果。由於驗證是在二維平麵上進行的,初始殘餘應力隻有一個方向。
實際加工驗證
為驗證所提方法在實際加工中的可行性,選取外型尺寸為640 mm × 240 mm × 26 mm的毛坯作為加工對象提取變形力,如圖所示11(a),並在仿真環境下建立相應的數值計算模型。實驗采用7050-T7451鋁合金。
工件的實際裝夾方法如圖所示11(a).在監測點1、2、3、4位置安裝測力夾具,測量工件的變形力。彈簧約束設置在仿真環境中相應的位置。點1、點2、點3為固定夾具,在仿真環境中相應位置設置固定約束,固定工件的空間位姿。
如圖所示11(a)、共7個槽,加工深度為22 mm,加工層數為11層,單次切割深度為2 mm。加工層數為11層,每層有7個槽。根據實際加工情況設置仿真環境。一層銑槽是一個分析步驟,總共有77個分析步驟。工件的切削深度為2mm,因此與實際工況相對應,厚度方向上的單元尺寸為1mm。從圖中所示的測點提取變形力11(a),工件變形力數據如圖所示12.根據理論驗證中采用的方法,在仿真環境中通過增加彈簧來獲得變形力。
根據本文提出的方法,圖中變形力數據對應的初始殘餘應力場12解決了。如圖所示13,經過連續迭代計算,計算結果最終收斂。
經過迭代求解,最小RMSE為6.71 n。按照與理論驗證相同的驗證思路,我們將求解結果與實際加工過程中監測的數據(即圖中真實值)進行比較14).對比結果如圖所示14結果表明,求解結果與實際加工監測數據吻合較好。我們計算了迭代解結果對應的平均相對誤差,結果表明平均相對誤差僅為9%。計算公式如下所示9):
在哪裏\({\三角洲}_{意味著}\)為平均相對誤差,地麵\ \ ({F} _ {_truth} \)為加工過程中監控的變形力,\ ({F} _{解決方案}\)求解結果對應的變形力;n是在實際加工中監測的變形力的大小。
初始殘餘應力的推斷結果是基於銑削深度為22 mm時的變形力。為了進一步驗證推斷結果的有效性,我們在22 mm的基礎上繼續銑削至23 mm,對比推斷結果對應的變形力與實際加工過程中監測到的變形力(即圖中真實值)的差異15).這意味著我們使用推斷的初始殘餘應力來預測未來的趨勢。數字15顯示了在銑削深度為23毫米時的變形力對比。經比較,1號監測點誤差(RMSE)為12.22 N, 2號監測點誤差(RMSE)為1.41 N, 3號監測點誤差(RMSE)為4.68 N, 4號監測點誤差(RMSE)為8.68 N。
由於初始殘餘應力對工件的主要影響是加工變形,這裏我們將求得的初始殘餘應力對應的變形與工件加工後的實際變形進行比較。加工完成後(銑削深度為23mm),我們釋放測力夾具對工件的約束,使工件變形。用機床自帶的探頭測量變形量(圖11(b)按圖中監測點所示的位置。11(a).工件初始殘餘應力引起的變形主要表現為翹曲,因此我們提取了在Z方向作為工件的變形。測量結果如表所示4.
如表所示4,求得的變形為本文方法得到的初始殘餘應力場對應的變形;地麵真值是在實際加工中測量到的變形量。從表中的數據4,可以看出解出的變形量與地麵真實值相差較小,實際變形量與解出的變形量最大誤差僅為0.0671 mm,平均誤差為0.0446 mm。通過驗證可以看出,推斷的結果能夠反映工件加工的變形趨勢,但與實際結果存在一定誤差。這部分誤差主要與有限元計算中網格尺寸有關。當網格尺寸較大時,誤差會增大,當網格尺寸較小時,誤差會相應減小。然而,網格尺寸的減小會直接導致計算量的增加,影響計算效率。本文根據實際誤差要求和計算效率選擇了網格尺寸。
討論
本文提出的初始殘餘應力場推斷方法是為了求解初始殘餘應力場的均值和方差。因此,求解結果存在不確定性。為了評價數據的不確定性,我們用置信度和置信區間來量化求解結果的可靠性,以保證數據表達信息的完整性。這裏我們以求解結果所對應的誤差為對象來評估不確定度。
首先,根據求解結果獲得初始殘餘應力樣本;這裏,本文的樣本數量為1000。其次,計算初始殘餘應力樣本對應的變形力;最後,將計算得到的變形力樣本與實際變形力樣本進行比較,得到樣本誤差。誤差分布如圖所示16.如圖所示16,誤差分布是傾斜的。置信區間[6.5,7.2]的置信值為95%。即結果的誤差有95%的概率落在6.5 N - 7.2 N之間。可以看出,當置信水平為95%時,求解結果的最大RMSE為7.2 N,對應的變形力如圖所示17.
在實際加工中,加工變形不僅受初始殘餘應力的影響,還受加工引起的殘餘應力的影響。該方法不考慮加工過程中產生的殘餘應力。這主要是因為在粗加工過程中,加工引起的殘餘應力隻分布在很小的加工表麵範圍內,尤其是鋁合金材料。Ref。36]表明在鋁合金加工過程中,殘餘應力的最大分布深度不超過0.1 mm。本文在粗加工階段對數據進行監測,且整個加工過程中零件的壁厚大於3 mm,因此可以忽略加工引起的殘餘應力的影響。在計算精加工殘餘應力場和難加工材料時,應考慮加工引起的殘餘應力的影響。
該方法推導出工件內部的全局初始殘餘場,可用於工件整體加工變形分析和工件加工變形控製。現有的傳統殘餘應力檢測方法大多隻能用於局部殘餘應力的檢測。中子衍射技術雖然具有較強的穿透能力,但在檢測整體殘餘應力時存在較大的誤差。因此,現有的測試結果不能有效地反映工件內部的整體初始殘餘應力水平。
該方法通過有限元分析軟件(ABAQUS)模擬實際加工過程,實現了殘餘應力場的迭代求解。當工件的幾何結構、加工路徑、裝夾布局等實際加工條件發生變化時,通過修改有限元分析條件可以推斷出不同加工條件下的殘餘應力場。
結論
為了推斷工件內部的初始殘餘應力場,本文提出了一種將監測數據與機構模型相結合來推斷毛坯初始殘餘應力場的方法。該方法以工件加工過程中的變形力為推斷依據,求解出坯料內部的初始殘餘應力場。最後,實驗驗證表明,變形力平均相對誤差為9%,加工平均變形誤差為0.0446 mm。計算結果能較好地反映工件內部的初始殘餘應力場,為結構件的變形控製提供了很好的依據。
綜上所述,本文的研究有以下貢獻:
首先,本文提出的方法可以從加工過程中的監測數據推斷工件內部的初始殘餘應力場;這為優化加工工藝、提高工件質量提供了有效的依據。
其次,利用神經網絡生成器隨機生成模擬初始殘餘應力,利用策略梯度法實現模擬誤差的梯度下降;因此,本文的研究也為有限元模擬的優化提供了思路。
最後,本文提出的方法是將在線監測數據與有限元仿真模型相結合的探索,為機器學習模型與機理模型的融合提供了研究參考。
雖然所提出的方法在實驗中可以有效地推斷出工件內部的初始殘餘應力,但仍有很多工作要做。本文僅在預拉伸板和鋁合金材料等初始殘餘應力場分布規律的坯料中得到了有效驗證。對於模具鍛件等結構複雜的毛坯,該方法仍麵臨許多挑戰。對於模鍛等毛坯,初始殘餘應力場的分布較為複雜。對於鈦合金等難加工材料,加工引起的殘餘應力不容忽視,仍需進一步研究。
參考文獻
B Denkena, D Boehnke, L D León。鋁結構件加工引起的殘餘應力。生產工程, 2008, 2(3): 247-253。
D Chantzis, S Van-Der-Veen, J Zettler,等。在航空航天工業加工大型整體式零件時,可將零件變形降至最低的工業工作流程。Procedia CIRP, 2013, 8: 281-286。
M C Santos, A R Machado, W F Sales,等。鋁合金加工綜述。國際先進製造技術雜誌, 2016, 86: 3067-3080。
馬蘇迪,阿米尼,賽伊迪,等。加工殘餘應力對薄壁零件變形的影響。國際先進製造技術雜誌, 2014, 76(1-4): 597-608。
鄭貴木,晁勇,陳紹仁。鈦合金(TC4)薄壁件銑削實驗研究。材料加工技術雜誌, 2003, 138(1-3): 489-493。
X Cerutti, K Mocellin。利用有限元法和大規模去除法預測殘餘應力引起的加工後變形。主要工程材料, 2014, 611-612: 1159-1165。
楊洋,金利,杜傑,等。7050-t7451鋁合金薄壁長縱杆運輸振動下的殘餘應力鬆弛。bwin900手机版, 2020, 33: 158-167。
J。單元化機身因殘餘應力引起的加工變形研究。機械工程學報, 2005, 41(2): 117-122。(中文)
袁曉明,張軍,連勇,等。鎂合金殘餘應力測定的研究進展。《鎂合金雜誌》, 2018, 6(3): 238-244。
A Yazdanmehr, H Jahed。用x射線衍射法測量鎂合金表麵殘餘應力。材料,2020年,13(22):5190。
詹勇,劉超,張建軍。激光超聲技術測量激光增材製造tc4鈦合金的殘餘應力。材料科學與工程:A, 2019, 762: 138093。
宋文濤,徐春光,潘慶賢,等。超聲波法無損檢測及殘餘應力場表征。bwin900手机版, 2016, 29(2): 365-371。
潘強,潘榮,邵c,等。螺栓軸向應力超聲測量原理與方法的研究進展。bwin900手机版, 2020, 33: 44-59。
D Kaisheva, G Bokuchava, I Papushkin等。低碳鋼電子束焊接殘餘應力的中子衍射測量。Comptes Rendus de l'Académie保加利亞的科學:科學Mathématiques et Naturelles地球物理學報,2020,73(4):475-484。
張永康,馮安祥,盧建忠,等。用x射線應力分析儀對aisi 304基板上鍍錫薄膜殘餘應力進行無損測量。國際光學工程學會學報, 2006年。
M R Viotti, A Albertazzi, P Staron,等。FHPP焊接殘餘應力場的測量:DSPI結合鑽孔和中子衍射的比較。有光學測量, 2013年。
劉海燕,徐春光,宋文濤,等。基於超聲檢測的閥塊殘餘壓應力恒定的研究。應用力學與材料, 2014, 494-495: 655-658。
潘迪,張誌強,張誌強,等。通過厚度殘餘應力場評估殘餘應力的新型殘餘應力測量技術。材料的信件, 2020, 277: 128347。
麥克斯韋爾,特恩布爾。用鑽孔技術測量工程塑料殘餘應力。聚合物測試, 2003, 22(2): 231-233。
劉立波,孫建峰,陳偉勇,等。7075T651鋁合金板材初始殘餘應力分布研究。中國機械工程, 2016, 27(4): 537-543。(中文)
德田德昌,王瑞光,木戶M,等。用壓痕法測量結構陶瓷的殘餘應力。主要工程材料, 2005, 297-300(Pt1): 515-520。
P Pagliaro, M B Prime, H Swenson,等。采用等高線法和多次切割測量多個殘餘應力分量。實驗力學, 2010, 50(2): 187-194。
王F,毛凱,李B。從表麵應力測量中預測殘餘應力場。國際機械科學雜誌, 2018: 68 - 82。
王芳,毛凱,吳勝,等。基於二元傅裏葉級數的局部點應力表麵殘餘應力場預測。數學與固體力學, 2018, 24(4): 979-995。
M I Hatamleh, J Mahadevan, A Malik,等。選擇性激光熔煉A357鋁合金激光衝擊強化殘餘應力場的預測。製造科學與工程雜誌, 2019, 141(10): 609-636。
朱康J R,吳國勇,菲茨帕特裏克M E,等。采用迭代法重建對焊板實驗測量的殘餘應力場,並與焊接過程模擬進行比較。國際機械科學雜誌、2019、160:421 - 428。
G H Farrahi, S A Faghidian, D J Smith。焊接板殘餘應力場的反演重建方法。壓力容器技術雜誌, 2010, 132(6): 1521-1523。
O Ozmen, C Sinanolu, A Caliskan,等。基於深度神經網絡的圓窩軸向柱塞泵滑靴泄漏預測。bwin900手机版, 2020, 33: 119-129。
B M Lake, R Salakhutdinov, J B Tenenbaum。通過概率程序歸納的人類層次的概念學習。科學, 2015, 350(6266): 1332-1338。
徐坤,李永光,劉長強,等。在數據驅動的製造過程中先進的數據收集和分析。bwin900手机版, 2020, 33: 40-60。
N Ruiz, S Schulter, M Chandraker。學習模擬。國際學習表征會議, 2019年。
M Raissi, P Perdikaris, G Karniadakis。物理信息神經網絡:用於解決非線性偏微分方程的正問題和反問題的深度學習框架。計算物理雜誌, 2019, 378: 686-707。
M盧特,C裏特,J彼得斯。深度拉格朗日網絡:使用物理作為深度學習之前的模型。https://arxiv.org/abs/1907.04490(2021-08-03)。
S Greydanus, M Dzamba, J Yosinski。哈密頓神經網絡。https://arxiv.org/abs/1906.01563(2021-08-03)。
趙誌偉,李永貴,劉長青,等。基於變形力數據的物理潛變量模型預測零件變形。機器人與計算機集成製造地球物理學報,2021,72:102204。
黃X。鋁合金整體構件銑削變形機理及預測。濟南:山東大學,2015。(中文)
R·威廉姆斯。連接主義者強化學習的簡單統計梯度跟隨算法。機器學習, 1992, 8(3-4): 229-256。
確認
不適用。
資金
國家自然科學基金(批準號:51775278)和國家傑出青年科學基金(批準號:51925505)資助。
作者信息
作者和聯係
貢獻
概念化,方法論,形式分析,撰寫原始草案,驗證。概念,方法,監督,項目管理。CL:概念化、驗證、可視化、調查、形式分析、寫作審查和編輯。形式分析、可視化、數據管理。所有作者閱讀並批準最終稿。
作者的信息
王樹國,現任碩士研究生南京航空航天大學機電工程學院,中國.主要研究方向為智能製造。
李英光,現任教授南京航空航天大學機電工程學院,中國主要研究方向為智能數控加工、複合材料新原理固化技術及設備。
劉長青,現任教授南京航空航天大學機電工程學院,中國.主要研究方向為數字製造、智能製造。
趙誌偉,現任博士研究生南京航空航天大學機電工程學院,中國.主要研究方向為數字製造、智能製造。
相應的作者
道德聲明
相互競爭的利益
作者聲明沒有競爭的經濟利益。
權利和權限
開放獲取本文根據知識共享署名4.0國際許可協議授權,該協議允許以任何媒介或格式使用、共享、改編、分發和複製,隻要您適當地注明原作者和源代碼,提供知識共享許可協議的鏈接,並說明是否進行了修改。本文中的圖像或其他第三方材料均包含在本文的知識共享許可中,除非在材料的信用額度中另有說明。如果材料不包含在文章的知識共享許可中,並且您的預期使用不被法定法規允許或超過允許的使用,您將需要直接從版權所有者獲得許可。如欲查閱本牌照副本,請瀏覽http://creativecommons.org/licenses/by/4.0/.
關於這篇文章
引用這篇文章
王鬆,李暘,劉超。et al。一種結合監測數據和機理模型的初始殘餘應力推斷方法。下巴。j .機械工程。Eng。35歲,82(2022)。https://doi.org/10.1186/s10033-022-00746-9
收到了:
修改後的:
接受:
發表:
DOI:https://doi.org/10.1186/s10033-022-00746-9
關鍵字
- 初始殘餘應力
- 推理
- 監控數據
- 機理模型
- 政策梯度